1 引 言 先進復(fù)合材料由于其優(yōu)越的性能而越來越多地被廣泛應(yīng)用于現(xiàn)代飛機結(jié)構(gòu)中。而目前,在飛行器的復(fù)合材料重要受力結(jié)構(gòu)件之間,機械連接仍是主要的連接方式,并且大多采用多釘連接的形式。針對多釘連接強度的分析計算是提高連接效率,充分發(fā)揮復(fù)合材料應(yīng)用性能的主要手段之一。近年來,國內(nèi)外學(xué)者多致力于利用累積損傷模型精確模擬復(fù)合材料單釘連接結(jié)構(gòu)的損傷演化過程和強度計算。但是,由于多釘連接結(jié)構(gòu)在承載過程中存在大量幾何非線性、材料非線性和狀態(tài)非線性的問題,利用累積損傷方法分析的過程中,受計算成本和收斂性的困擾,目前針對多釘連接強度的研究較少,大多數(shù)停留在釘載分配的研究階段。 針對上述研究現(xiàn)狀,本文借鑒顯式算法在求解復(fù)合材料層合板沖擊后壓縮的準(zhǔn)靜態(tài)問題時的思路,并且結(jié)合顯式算法在求解存在復(fù)雜接觸及非線性的準(zhǔn)靜態(tài)問題中不存在收斂問題和計算成本小的優(yōu)點,文中利用顯式算法求解復(fù)合材料層合板多釘 連 接 件 的 拉 伸 強 度。 計 算 過 程 中,采 用ABAQUS 的子程序 VUMAT編寫三維 Hashin失效準(zhǔn)則,結(jié)合剛度一次退化的累積損傷模型( 后文簡稱剛度一次退化模型) ,利用 ABAQUS /Explicit 顯式算法進行復(fù)合材料層合板多釘連接件的損傷演化和強度分析。同時,進行了復(fù)合材料層合板多釘連接件的雙剪拉伸試驗。 2 有限元模型 復(fù)合材料層合板多釘連接結(jié)構(gòu)的三維有限元建模及分析在 ABAQUS 中實現(xiàn),材料基本性能、本構(gòu)關(guān)系、失效準(zhǔn)則和剛度退化模式的定義通過編寫子程序 VUMAT 實現(xiàn)。有限元建模過程中,不考慮兩端玻璃鋼加強片區(qū)域。鈦合金板和螺栓、螺母采用 8 節(jié)點六面體線性減縮積分單元 C3D8R,螺栓和螺母作為一個整體建模,復(fù)合材料層合板采用 8 節(jié)點六面體線性減縮積分單元 C3D8R,在螺栓柱與孔之間、板與板之間、螺栓帽與板之間等多個實際接觸面均建立接觸。沿厚度方向分為 n 層,n 代表復(fù)合材料層合板的總的層數(shù)。由于損傷的非對稱性,利用全模型計算,圖 1 為多釘連接結(jié)構(gòu)的有限元網(wǎng)格圖。模型總共有65568 個單元,孔邊主要應(yīng)力分析區(qū)域單元最小尺寸為 0. 427mm,單元厚度為 0. 125mm。從距離復(fù)合材料層合板自由端算起,3 個釘?shù)木幪栆来螢?B1、B2、B3。
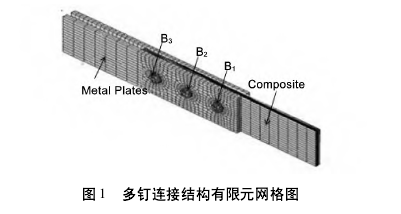
2. 1 失效準(zhǔn)則和材料剛度退化 本文選用三維 Hashin 失效準(zhǔn)則,相比較二維Hashin 準(zhǔn)則,增加了非線性項,并強調(diào)了剪切模式對損傷的重要性,將剪切模式獨立考慮,從而將二維 Hashin 準(zhǔn)則中的 4 種損傷模式擴展到了 5 種,并且將原列式右端的常數(shù)項用損傷指標(biāo)表示。本文認(rèn)為,損傷指標(biāo)大于等于 1 時,即認(rèn)為單元失效。根據(jù) Tsai 等研究結(jié)果,非線性剪切本構(gòu)關(guān)系具有如下形式:

其中,G12、τ12、γ12分別代表初始剪切模量、剪切應(yīng)力和剪切應(yīng)變,α 是由試驗決定的常數(shù)。根據(jù) 單 向 板 試 驗 的 應(yīng) 力 應(yīng) 變 曲 線, 擬 合 得到α = 8. 334 × 10- 6MPa- 3。與 5 種失效準(zhǔn)則相對應(yīng),每種基本失效模式所對應(yīng)的材料退化方式如表 1 所示。
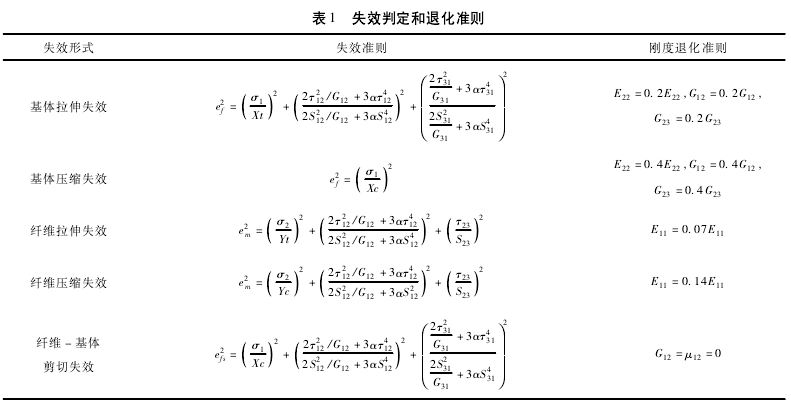
2. 2 接觸狀態(tài)非線性 接觸問題屬于邊界條件非線性問題,運用有限元分析理論來求解接觸問題,一般包含以下特點:接觸過程既有由接觸面積變化而產(chǎn)生的非線性以及由接觸壓力分布變化而產(chǎn)生的非線性,也有由摩擦作用產(chǎn)生的非線性。這些特點決定了接觸問題通常采用增量方式求解。 而接觸面的范圍和接觸狀態(tài)屬于未知量,此特點決定了接觸問題需要采用試探 - 校核的迭代方法求解。通常,將接觸界面條件引入求解方程的方法有兩種: 拉格朗日乘子法和罰函數(shù)法。與拉格朗日乘子法相比,用罰函數(shù)法引入接觸界面約束條件的優(yōu)點是不增加問題的自由度,并且使求解方程的系數(shù)矩陣保持正定。因為不增加問題的自由度,可以和利用顯式數(shù)值積分方法求解包含慣性項的接觸問題時的求解方程相協(xié)調(diào)。由于系數(shù)矩陣保持正定,在靜力求解接觸問題時,可以避免由于系數(shù)矩陣非正定性可能出現(xiàn)的麻煩。 因此,本文使用罰函數(shù)法求解接觸問題。定義接觸屬性為有限滑移,在顯式分析中,有限滑移也是通用接觸算法的唯一選項,即兩個接觸面之間可以有任意的相對的滑動,允許接觸面之間任意大的滑動和旋轉(zhuǎn)。在有限滑移分析中,ABAQUS 會自動地判斷從面節(jié)點和主面哪一個部分發(fā)生接觸。 2. 3 準(zhǔn)靜態(tài)模擬的判定 評估模擬是否產(chǎn)生了正確的準(zhǔn)靜態(tài)響應(yīng),最具有普遍意義的方式是研究模型中的各種能量。下面是在ABAQUS /Explicit 中的能量平衡方程: EI+ EV+ EKE+ EFD- EW= Etotal= constant ( 2) 式中,EI是內(nèi)能( 包括彈性和塑性應(yīng)變能) ,EV是粘性耗散吸收的能量,EKE是動能,EFD是摩擦耗散吸收的能量,EW是外力所做的功,Etotal是在系統(tǒng)中的總能量。在一個準(zhǔn)靜態(tài)的事件中,比如一個單軸拉伸試驗,如果模擬是準(zhǔn)靜態(tài)的,那么外力所做的功幾乎等于系統(tǒng)內(nèi)部的能量。除非有粘彈性材料、離散的減振器,或者使用了材料阻尼,否則粘性耗散能量一般是很小的。在準(zhǔn)靜態(tài)過程中,慣性力可以忽略不計。由此可以推論,動能也是很小的。作為一般性的規(guī)律,在大多數(shù)過程中,變形材料的動能將不會超過其內(nèi)能的一個小的比例( 典型的為 5% 到10% ) 。數(shù)值模擬中,滿足動能維持在內(nèi)能的一個小比例范圍內(nèi),就可以認(rèn)為該準(zhǔn)靜態(tài)模擬是合理的。 3 多釘雙剪拉伸試驗 拉伸試驗在 MTS810 Teststar ± 100kN 液壓伺服材料試驗系統(tǒng)上進行,試驗溫度為室溫。在試驗過程中,記錄每個試驗件的破壞載荷和破壞模式( 可能的破壞模式有擠壓破壞、截面拉斷、緊固件剪斷、緊固件拉脫等) 。復(fù)合材料層壓板為對稱均衡鋪層形式,單層厚度為 0. 125mm,有 兩 種 鋪 層 類 型,分 別 是[45 /0 /- 45 /90 /45 /0 / - 45 /0 ]s、[45/0/ - 45/90/45/0/- 45 /0]2s,厚度分別為 2mm 和 4mm。雙剪時,金屬搭板在外側(cè),中間板為層壓板,金屬板和層壓板名義厚度相同。兩種厚度的復(fù)合材料層合板編號分別為 SDSJ - 1( 層合板厚度 2mm) 和 SDSJ - 2( 層合板厚度 4mm) ,多釘雙剪試件的幾何參數(shù)和螺栓直徑見圖 2 和表 2。復(fù)合材料板的纖維體積含量約為62% ,單向?qū)訅喊寤玖W(xué)性能見表 3。金屬板和螺栓 彈 性 模 量 E = 116GPa,泊 松 比 μ = 0. 3,σb= 900MPa。
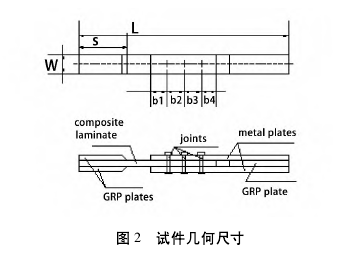
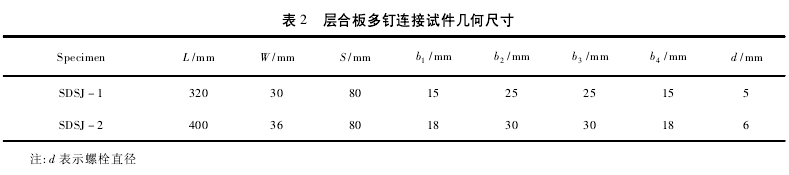
 試驗結(jié)果為,SDSJ-1 最終破壞載荷為 26. 3kN,SDSJ-2 最終破壞載荷為 60. 1kN。 4 數(shù)值計算結(jié)果與分析討論 以試件 SDSJ - 1 為 例,圖 3 為 加 載 速 率 為30mm / s 下的動能與內(nèi)能曲線圖。從圖中可以看出,動能與內(nèi)能比小于 10% 。結(jié)合本文 2. 3 的準(zhǔn)靜態(tài)模擬過程的判定依據(jù),可以認(rèn)為,利用顯式算法計算多釘連接強度的數(shù)值模擬過程是準(zhǔn)靜態(tài)過程,符合實際的準(zhǔn)靜態(tài)加載過程。圖中拐點表示連接件失去承載能力,內(nèi)能突然下降。其它試件的計算結(jié)果類似,動能與內(nèi)能的比值均小于 10% ,由于篇幅有限,此處不再贅述。
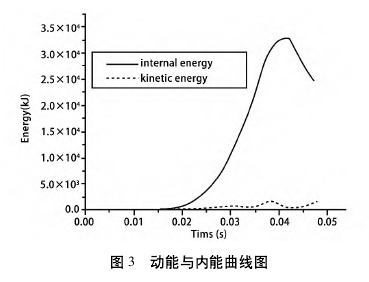
以 SDSJ - 2 為例,給出數(shù)值模擬的計算結(jié)果。通過累積損傷方法結(jié)合顯式算法,最終的有限元輸出結(jié)果如圖 4 所示,為復(fù)合材料多釘雙剪結(jié)構(gòu)的載荷 - 位移曲線圖。圖中,橫坐標(biāo)為層合板端部軸向平均位移,縱坐標(biāo)為支反力軸向分量。隨著拉伸位移的增大,開始階段保持較好線性,在接近失效前出現(xiàn)非線性變化。當(dāng)載荷隨位移下降時,即表明結(jié)構(gòu)不能再承受外載,即達到強度極限。通過載荷 -位移曲線,可以確定多釘連接件的最終拉伸強度。誤差計算如式( 3) 所示,誤差計算結(jié)果如表 4 所示。
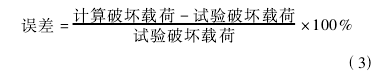
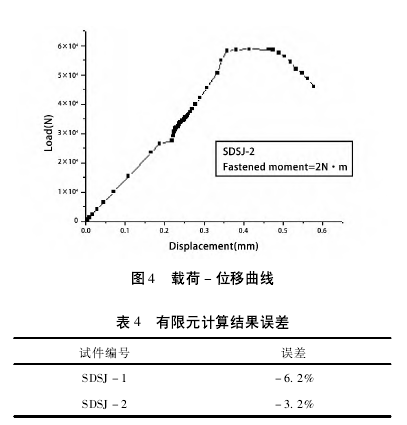
利用子程序 VUMAT 編寫的剛度一次退化模型結(jié)合顯式算法計算多釘雙剪連接件的破壞載荷,最大誤差不超過 7% ,比較準(zhǔn)確,結(jié)果總體偏于保守。這可能是由于所采用的三維 Hashin 失效準(zhǔn)則中考慮到了層間應(yīng)力對損傷的影響。同時,由于纖維拉伸破壞判據(jù)包含剪切應(yīng)力項,當(dāng)螺栓連接孔邊 45°處存在較大的剪切應(yīng)變時,失效準(zhǔn)則過高地估計了剪切應(yīng)變對纖維斷裂的影響,導(dǎo)致?lián)p傷較早地出現(xiàn),降低了最終破壞載荷值。 5 結(jié) 論 利用顯式算法計算多釘連接件強度過程中,由于動能和內(nèi)能比值小于 10% ,因此,認(rèn)為數(shù)值模擬過程是準(zhǔn)靜態(tài)加載,符合實際情況。同時,利用顯式算法結(jié)合子程序編寫的剛度一次退化的累積損傷模型,計算得到連接件的失效載荷,與試驗結(jié)果相比,誤差最大不超過 7% 。通過計算結(jié)果發(fā)現(xiàn),利用三維 Hashin 失效準(zhǔn)則作為單元失效的判據(jù),得到的結(jié)果偏保守,這可能是由于準(zhǔn)則中考慮到了層間應(yīng)力對損傷的影響。同時,由于纖維拉伸斷裂判據(jù)包含剪切應(yīng)力項,當(dāng)螺栓連接孔邊 45°處存在較大的剪切應(yīng)變時,失效準(zhǔn)則過高地估計了剪切應(yīng)變對纖維斷裂的影響,從而導(dǎo)致?lián)p傷較早地出現(xiàn),降低了最終破壞載荷值。
|