1. 引 言 某水下航行體在發(fā)射出筒后,在水中豎直向上運(yùn)動,出水后在空中自由飛行,到達(dá)最高點(diǎn)后下落,然后在水中下沉,到達(dá)最低點(diǎn)后再上浮,最后漂浮在水面上。航行體回落入水后,可能發(fā)生與發(fā)射裝置碰撞的危險。出于安全性的考慮,航行體在水下發(fā)射后必須進(jìn)行減速控制,并使其速度保持在一定范圍,從而間接地保證回落入水的最大深度小于發(fā)射裝置最高點(diǎn)的深度。舵板是實(shí)現(xiàn)此功能的重要部件,當(dāng)水下航行體以一定速度進(jìn)入水中時,舵板迅速張開至一定角度,增加航行體在水中的阻力,對航行體進(jìn)行減速控制。在減速過程中,舵板在水流的沖擊下迅速張開,在到位的瞬間突然制動,舵板承受了巨大的水動力沖擊載荷,舵板本體和耳座處均產(chǎn)生很大的沖擊應(yīng)力及應(yīng)變( 見圖 1) 。卸載后,彈性變形恢復(fù),塑性變形及部分應(yīng)力殘余在結(jié)構(gòu)中。出于經(jīng)濟(jì)性和安全性的考慮,需要評估舵板及其系統(tǒng)主要零部件在多次過載后的剩余沖擊壽命。在應(yīng)變分析和低周疲勞的基礎(chǔ)上,現(xiàn)采用一種新的疲勞壽命估算方法———局部應(yīng)力應(yīng)變法,此法思路是: 零構(gòu)件的疲勞破壞都是從應(yīng)變集中部位的最大應(yīng)變處起始,并且在裂紋萌生以前都要產(chǎn)生一定的塑性變形,局部塑性變形是疲勞裂紋萌生和擴(kuò)展的先決條件。因此,決定零構(gòu)件疲勞強(qiáng)度和壽命的是應(yīng)變集中處的最大局部應(yīng)力和應(yīng)變。其基本假設(shè)是: 若同種材料制成構(gòu)件的危險部位最大應(yīng)力應(yīng)變歷程與一個光滑試件的應(yīng)力應(yīng)變歷程相同,則它們的疲勞壽命就相同。
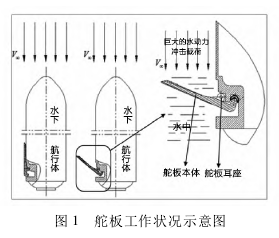
因此,本文針對有應(yīng)力集中部件的疲勞壽命,通過對其光滑試件進(jìn)行沖擊疲勞試驗(yàn),確定沖擊次數(shù),對結(jié)構(gòu)的使用壽命進(jìn)行預(yù)測。 2 試件制備與試驗(yàn)方法
2. 1 試件制備 2. 1. 1 取樣位置確定 本文選取受到 3 次入水沖擊后的舵板作為試驗(yàn)對象,其材料為 18Cr2Ni4WA,試件取樣位置如圖 2所示。
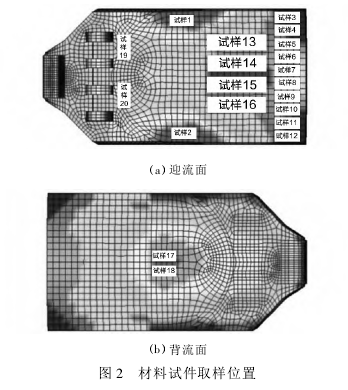
2. 1. 2 試件制備 按照 GB /T229-2007《金屬材料 夏比擺錘沖擊試驗(yàn)方法》對圖 2 所示的試件號 6、7、8、9,進(jìn)行標(biāo)準(zhǔn)夏比 V 型缺口試驗(yàn)。對試件號 1、2、3、4、5、10、11、12、17、18 進(jìn)行標(biāo)準(zhǔn)無缺口加工,試件加工尺寸參看圖 3 和圖 4。缺口加工方法采用定型砂輪磨制或銑床加工,缺口部位應(yīng)避免劃傷。應(yīng)變片貼于試件中部,所有試件制備情況見圖 5。
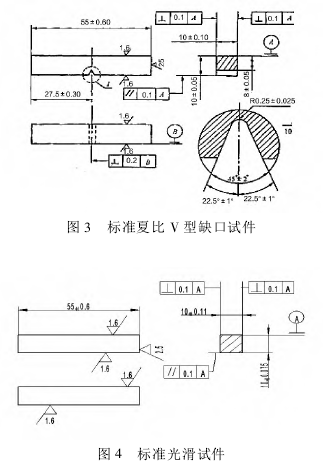
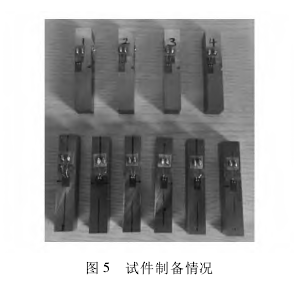
2. 2 試驗(yàn)方法 2. 2. 1 試驗(yàn)設(shè)備 及原理采用的試驗(yàn)設(shè)備為美國 MTS 公司 ZBC2000 系列( 最大沖擊能 300J) 擺錘沖擊試驗(yàn)機(jī)( 見圖 6) ,其控制系統(tǒng)采用 PLC 控制方法。該設(shè)備由旋轉(zhuǎn)編碼器來獲取擺錘的實(shí)時位置,具有抗干擾能力極強(qiáng),可靠、穩(wěn)定、數(shù)據(jù)準(zhǔn)確等特點(diǎn)。采用單向應(yīng)變計(jì),型號為 BX120-10AA,測試系統(tǒng)的量程為 20000με,超過該范圍的數(shù)值不作為評價依據(jù),僅供參考。應(yīng)變測試采用 DASP -V10 動態(tài)應(yīng)變采集系統(tǒng)。試驗(yàn)方法為: 將試件放置在砧座上,通過設(shè)定擺錘的沖擊能對試件進(jìn)行不同能量的沖擊試驗(yàn),觀察試件的斷裂及變形情況( 見圖 7) 。本次試驗(yàn)對于含缺口試件進(jìn)行一次沖擊,對于光滑試件進(jìn)行多次沖擊,觀察沖擊后的試件宏觀形變與微觀應(yīng)變特征。
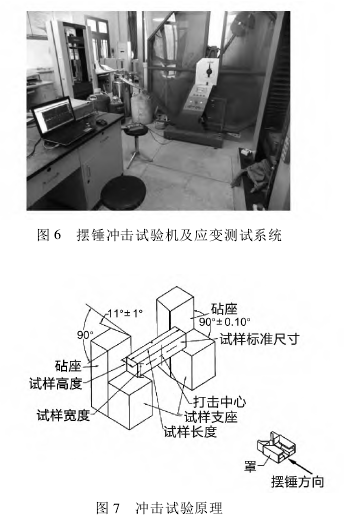
2. 2. 2 沖擊能量確定 擺錘大能量沖擊理論是根據(jù)應(yīng)力應(yīng)變法的基本假設(shè),即若同種材料制成的構(gòu)件的危險部位的最大應(yīng)力-應(yīng)變歷程與一個光滑試件的應(yīng)力應(yīng)變歷程相同,則它們的疲勞壽命就相同。因此,在按照國標(biāo)進(jìn)行擺錘沖擊試驗(yàn)時,沖擊能量的確定是依據(jù)實(shí)際工況中舵板上危險部位的應(yīng)變水平。根據(jù)前期仿真結(jié)果,選取模型中舵板厚度變化處、等效應(yīng)力相對較大的某個單元,測得其應(yīng)力峰值可達(dá)到 0. 85GPa 左右。根據(jù)該單元的應(yīng)力、應(yīng)變分量,計(jì)算其應(yīng)變能為:
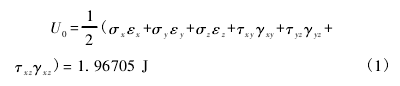

按照該應(yīng)變能密度計(jì)算,舵板的總應(yīng)變能最多應(yīng)為 10. 55kJ,大于直接測得的真實(shí)總內(nèi)能( 應(yīng)變能) ,峰值為 7. 082kJ,即:

這說明,使用應(yīng)變能密度 458. 7 kJ/m3作為從大尺度舵板到小尺度擺錘沖擊試驗(yàn)件進(jìn)行尺度和沖擊能量縮放依據(jù),具有一定的可比性。 根據(jù)國標(biāo),光滑無缺口的沖擊試件的體積為:

使得光滑無缺口的沖擊試件達(dá)到 0. 85GPa 的等效應(yīng)力水平時需要吸收的應(yīng)變能為:

通過對舵板應(yīng)變較大危險點(diǎn)的應(yīng)變進(jìn)行實(shí)測,直接得到了 0°、90°和 45°方向的應(yīng)變。當(dāng)測量時間t = 19. 58s 時,3 方向的最大應(yīng)變分別為:
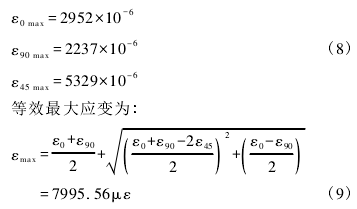
首先對光滑試件預(yù)試驗(yàn)沖擊,得到當(dāng)用 6J 能量對光滑試件進(jìn)行沖擊時,應(yīng)變片粘貼處的實(shí)測應(yīng)變?yōu)?8753. 966με,大于公式中危險點(diǎn)的 7995. 56με,表明 6J 沖擊能量剛好接近實(shí)測工況下的舵板受載情況。為研究不同能量沖擊對舵板的影響,沖擊試驗(yàn)時分別選取了 6J、8J、10J、15J 和 20J 等 5 種能量進(jìn)行多次沖擊。
|